시스템 자동화로 리큐어의 풍미 극대화
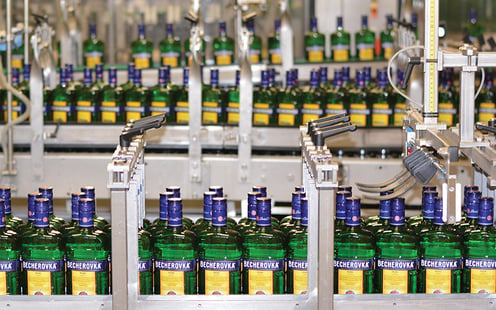
약초 맛이 감도는 베체로브카(Becherovka) 리큐어의 200년 된 제조법은 일급 비밀입니다. 세간에는 체코 카를로비 바리(Karlovy Vary) 마을의 13호 광천이 맛의 원천이라는 풍문이 돌고 있습니다. 하지만 이 회사의 주입 및 패키징 시스템이 COPA-DATA의 zenon 소프트웨어 기반 공정 제어 시스템으로 운영된다는 소문은 풍문이 아니라 분명한 사실입니다. 이 시스템은 이 저명한 리큐어 제조사가 효율성 향상을 위한 토대를 제공합니다.
Jan Becher - Karlovarská Becherovka의 공정 제어 시스템으로 사용되는 zenon
- 중앙집중식 시스템 모니터링
- 수동 데이터 수집의 수고로움 및 평가 시스템 파편화 제거
- 전체 장비 효율성(OEE) 평가
- 다운타임 및 속도 변화 평가, 파레토 차트 지원
- 포괄적이고 자동화된 공정 보고
체코 공화국의 카를로비 바리(독어명: 카를스바트)는 세계적인 스파 리조트로 오랜 명성을 자랑합니다. 14세기부터 12곳의 온천에서 뿜어져 나오는 약용수가 온천욕에 사용되었고, 16세기부터는 음용수로도 활용되기 시작했습니다. 13호 광천은 1807년, 요세프 비투스 베헤르(Josef Vitus Becher)가 원래 약용으로 약초 리큐어를 개발하면서 만들어졌습니다. 줄어든 쓴맛으로 이 리큐어는 많은 애주가 사이에서 빠르게 인기를 얻었습니다. 베체로브카(Becherovka)라는 이름의 이 리큐어는 보헤미아 전통 요리의 필수 재료로 자리매김했으며, 구색을 갖추고 있는 바에서는 쉽게 찾아볼 수 있습니다.
19세기에 이르러 Jan Becher는 산업 규모로 리큐어를 생산하여 전 세계에 수출하기 시작했습니다. 세계 최대 증류주 제조업체인 페르노리카(Pernod Ricard)가 2001년부터 이 회사를 소유하고 있습니다. 과거 생산 공장은 현재 박물관으로 대중에게 공개되고 있으며, 제품은 2010년 카를로비바리 외곽에 개장한 공장에서 생산되고 있습니다.
숙성은 오래, 보틀링은 짧게
베체로브카 한 배치를 생산하는 데에는 90일에서 100일이 소요됩니다. 먼저 전 세계에서 공급된 20여 종의 약초는 “약실”에서 일급 기밀 제조법에 따라 혼합됩니다. 약초 혼합물은 다소 큰 사이즈의 티백에 담긴 후, 순수한 알코올이 담긴 밀폐용기에서 1주일 동안 보관되며, 뜨거운 상태에서 서서히 냉각됩니다. 물과 설탕 등 다른 재료가 알코올에 첨가되고 리큐어를 오크 통에 옮겨 담은 후, 2개월간 숙성됩니다.
이후 여과를 거쳐 약초 리큐어를 -5°C로 냉각시킨 다음, 중앙 주입 라인으로 이송합니다. Jan Becher - Karlovarská Becherovka의 플랜트 디렉터인 토마시 브리즈갈(Tomáš Bryzgal)은 “베체로브카는 5cc의 미니어처 사이즈부터 잘 알려진 3리터 납작 유리병에 이르기까지 다양한 사이즈로 생산된다”며, “빈 병을 팔레트에서 제거하는 것에서부터 채워진 병을 팔레트화하고 라벨을 붙이는 작업, 주세 증지를 부착하는 작업까지 전체 주입 공정이 고도의 자동화를 통해 이루어진다”고 밝혔습니다.
수기 문서 작성 및 추정이 오류의 원인
10개의 시스템 섹션에는 각각 개별 컨트롤러가 장착되어 있습니다. 주입 라인이 처음 설치된 직후에는 간단한 하드웨어 인터페이스로 유닛을 서로 연결했습니다. 토마시 브리즈갈 씨는 “이 구성은 통상적인 운영 기간 내에는 원활하게 작동했다. 하지만 시스템 다운타임 등 문제가 발생하면 중앙에서 정보에 접근하기 힘들어 어려움이 발생하곤 했다”고 이야기합니다.
이러한 상황에서는 다운타임의 원인을 신속하게 파악하기가 어렵습니다. 문제 해결 과정이 지연될 뿐만 아니라, 나중에 시스템의 효율성을 계산하는 것도 어려워집니다. 생산 현장의 직원들이 시스템 다운타임에 대한 정보를 일일이 손으로 기록해야만 했습니다. 토마시 브리즈갈 씨는 “장애가 난 부분을 찾고 수리를 진행하는 동안 정보를 기록했기에 정보가 항상 정확하진 않았다”며, “특히 다운타임 시간은 온전히 기억을 더듬는 추정치였기에 부정확했다”고 말합니다.
또한 손으로 작성한 기록을 평가하기 위해 스프레드시트 형식으로 전송해야 하는 불편을 감소해야 했으며, 스프레드시트 형식은 분석을 위해 제한된 옵션만 제공했습니다. 그리고 무엇보다 회사 IT 팀과 자동화 시스템 모두에서 데이터와 평가 간의 괴리가 발생해 측정 제어에 쉽게 사용할 수가 없었습니다.
유연한 모니터링 시스템의 필요성
시스템의 효율성 모니터링을 개선하고 높은 수준으로 유지하기 위해 경영진은 파편화된 데이터 시스템을 전체가 통합된 최신 솔루션으로 교체하기로 결정했습니다. 이를 위해서는 충진 및 패키징 시스템을 아우를 수 있는 공정 제어 시스템이 필요합니다. 이미 잘 작동하고 있는 하위 시스템을 변경하지 않기 위해서는 해당 시스템의 PLC 프로그래밍을 방해하지 않으면서 솔루션을 구축해야 했습니다.
요구 조건은 광범위했습니다. 시스템이 주입 및 패키징 시스템 전반을 모니터링하고 전체 장비 효율성(OEE: Overall Equipment Effectiveness)를 평가할 수 있어야 했습니다. 별다른 수고로움 없이도 보고서에 다운타임 및 초 단위 다운타임(10초 이내)에 대한 평가 내용을 모두 담고 이를 파레토 차트로 표시할 수 있어야 했습니다. 위치와 관계없이 웹 서버를 통해 시스템에 액세스 가능하고 무단 액세스로부터 시스템을 보호해주는 RFID 로그인도 구축해야 했습니다.
개방형 소프트웨어 솔루션으로 완벽한 조정
체코의 헤프(Cheb)에 지사를 두고 있는 Kropf Solutions가 이 프로젝트의 수주를 받게 되었습니다. Kropf Solutions는 20년 넘게 COPA-DATA와 긴밀히 협력해 온 산업 자동화 전문 회사입니다. 이 프로젝트의 리더인 Kropf Solutions의 기술 부문 최고 담당자 로니 두헤크(Ronny Duchek)는 “zenon은 유연하고 개방적이며 신뢰할 수 있는 애플리케이션에 적합한 소프트웨어”라며, “이 든든한 토대를 기반으로 고객을 위해 매우 역동적이고 인체공학적인 맞춤 솔루션을 구축할 수 있었다”고 말합니다.
Jan Becher 통합 솔루션의 최우선 과제는 주입 및 패키징 시스템 내 모든 하위 시스템을 그룹화하여 게이트웨이를 통해 포괄적인 이더넷 네트워크로 구현하는 것이었습니다. 생산 시스템을 zenon 서버에 연결하고 회사 네트워크와도 연결했습니다. 기계와 관련된 일에 직접 개입할 수 있도록 산업용 멀티 터치 패널도 준비했는데, 이 패널에는 사용자가 zenon에 로그인 할 때 사용되는 RFID 판독기도 장착되어 있습니다.
고객과 시스템 통합업체 모두 실제 운영용으로 릴리스하기 전에 zenon 프로젝트를 광범위하게 테스트했습니다. 테스트 중, 프로젝트 정의 단계에서 아무도 생각하지 못했던 새로운 요구 사항이 계속해서 생겨났습니다. 하지만 zenon의 개방적인 구조 덕분에 구축 완료 시점에서도 이러한 요구 사항을 쉽게 구축에 통합할 수 있었습니다. 결과적으로 Kropf Solutions는 짧은 테스트 단계를 통해 매우 실용적으로 사용할 수 있는 솔루션을 고객에게 제공할 수 있었습니다.
수고로운 수작업 없이 완전한 개요 제공
zenon 기반 공정 제어 시스템으로 기존의 수동 기록 과정이 더 이상 불필요해졌습니다. 완전한 자동화 시스템이 모든 시스템 컴포넌트에 대한 운영 상태를 빠짐없이 기록하며, 사람이 숫자를 옮기면서 발생하기 쉬운 인적 오류의 가능성도 제거되었습니다. 데이터의 직접 전송없이도 자동으로 기록된 후 데이터베이스에서 모든 유형의 평가에 즉시 사용할 수 있습니다.
이제 그룹 전체에서 표준화된 방식으로 전체 장비 효율성(OEE: Overall Equipment Effectiveness)이 계산됩니다. Kropf Solutions의 애플리케이션 전문가가 사전 정의된 수식을 기반으로 통합 zenon Logic PLC 시스템 내에 평가 프로그램을 만들었습니다. 이 정보는 실시간 개요나 추세 다이어그램 등 다양한 형식으로 제공됩니다. 생산 중인 기계의 패널은 물론 멀리 떨어진 사무실에서도 웹 클라이언트를 통해 확인할 수 있습니다. 다운타임이나 주입 라인 속도의 갑작스러운 감소도 상세 보기로 확인 가능하며, 파레토 차트로도 표시할 수 있습니다.
전체적인 생산 운영 및 제어에 필수적일 뿐 아니라 그룹 내 후속 결정의 기반이 되는 일일 및 월간 보고서도 자동으로 생성하여 전송할 수 있습니다.
더욱 높은 수준의 최적화를 위한 데이터베이스 구축
토마시 브리즈갈 씨는 “다재다능한 기능과 까다로운 요구 사항도 적용 가능한 유연성, 사용자 친화적인 디자인이 zenon의 장점”이라며, 다음과 같이 말했습니다. “zenon을 통해 생산 공정을 투명하게 개선하고 직원들이 더 이상 문서 작업을 할 필요가 없어졌습니다. 이제 이 시스템을 발판으로 생산 공정을 더욱 최적화하는 데 착수할 계획입니다.”
-
zenon 덕분에 Kropf Solutions의 엔지니어는 테스트 단계에서 발견된 요구 사항을 포함하여 우리의 모든 특정 요구 사항을 성공적으로 구현할 수 있었습니다.
Tomáš Bryzgal | Plant Director Jan Becher - Karlovarská Becherovka, A.S
Download
-
Success StoryBecherovka_SUS_KR.pdf