Anlagenautomatisierung für den vollen Likörgenuss (Tschechien)
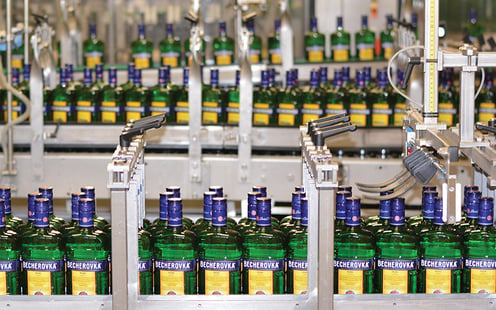
200 Jahre alt und streng geheim ist das Rezept des Kräuterlikörs Becherovka, der auch als 13. Karlsbader Heilquelle bezeichnet wird. Kein Geheimnis mehr ist die Effektivität der Abfüll- und Verpackungsanlage seit der Implementierung eines Leitsystems auf Basis der Software zenon von COPA-DATA. Dieses bildet die Grundlage für weitere Effizienzsteigerungen.
Highlights
- Zentrale Anlagenüberwachung
- Entfall manueller Datenerfassung und isolierter Auswertesysteme
- Auswertung der Gesamtanlageneffektivität (OEE)
- Auswertung der Stillstände und Geschwindigkeitsschwankungen inkl. Paretodiagramm
- Umfassendes, automatisiertes Reporting
Karlsbad (Karlovy Vary) in der Tschechischen Republik war lange Zeit der berühmteste und mondänste Kurort der Welt. Heilendes Wasser aus zwölf Quellen wird seit dem 14. Jahrhundert für Bäder, ab dem 16. Jahrhundert auch für Trinkkuren genutzt. 1807 erschloss man die 13. Quelle. Damals entwickelte Josef Vitus Becher einen ursprünglich als Medizin verwendeten Kräuterlikör. Keineswegs bitter fand dieser rasch eine treue Anhängerschaft. Unter dem Namen Becherovka ist das Getränk fester Bestandteil des kulinarischen Andenkens Böhmens. Der Likör darf in keiner gut sortierten Bar fehlen.
Seit dem 19. Jahrhundert stellt das Unternehmen Jan Becher den Likör im industriellen Maßstab her und exportiert ihn weltweit. Seit 2001 ist das Unternehmen Teil des weltgrößten Spirituosen-Herstellers Pernod Ricard. Während die alte Fabrik heute als Museum dient, erfolgt die Produktion in einem 2010 eröffneten Werk am Stadtrand von Karlsbad.
Langes Reifen, schnelles Abfüllen
Eine Charge Becherovka herzustellen, dauert 90 bis 100 Tage. Nach einem streng geheimen Rezept entsteht zunächst in der sogenannten Drogenkammer eine Mischung aus etwa 20 verschiedenen internationalen Kräutern. Verpackt in einer Art überdimensionalem Teebeutel, verbringen diese eine Woche in einem geschlossenen Behälter mit reinem Alkohol, zunächst heiß und dann langsam abkühlend. Nach dem Zusetzen weiterer Zutaten, in erster Linie Wasser und Zucker, reift der Likör zwei Monate lang in Eichenfässern.
Nach dem Filtrieren und einer kurzen Abkühlung auf -5 °C gelangt der Kräuterlikör in die zentrale Abfüllanlage. „Wir füllen Becherovka in Flaschen unterschiedlicher Größe, von Miniaturen mit fünf Zentiliter bis zu den bekannten, abgeflachten Flaschen mit bis zu drei Liter Fassungsvermögen“, sagt Tomáš Bryzgal, Produktionsdirektor von Jan Becher - Karlovarská Becherovka. „Vom Depalettieren der Leergebinde bis zum Palettieren der gefüllten, etikettierten und mit Steuerbanderolen versehenen Flaschen läuft der gesamte Vorgang mit einem hohen Automatisierungsgrad ab.“
Handschriftliche Dokumentation und Schätzungen als Fehlerquellen
Jede einzelne der zehn Teilanlagen ist mit einer individuellen Steuerung ausgestattet. Ihre Verkettung erfolgte seit der Installation der Abfüllanlage durch einfache Hardwareschnittstellen zwischen den Einheiten. „Im normalen Betrieb funktionierte diese Konfiguration sehr gut“, berichtet Bryzgal. „Schwierigkeiten verursachte der Mangel an zentral abrufbaren Informationen im Problemfall, z. B. bei Anlagenstillständen.“
In solchen Fällen war es oft nicht leicht, die Ursache für das Anhalten rasch festzustellen. Das verzögerte nicht nur die Störungsbehebung, sondern erschwerte auch die spätere Berechnung der Anlageneffektivität. Die Produktionsmitarbeiter erfassten handschriftlich die Informationen über jeden Anlagenstillstand. „Da sie die Aufzeichnungen parallel zu Fehlersuche und -behebung erfassten, waren diese nicht immer ganz exakt“, weiß Bryzgal. „Speziell die Stillstandszeiten waren oft recht ungenau, da es sich meist um nachträgliche Schätzungen handelte.“
Unbefriedigend war auch die Notwendigkeit, diese handschriftlichen Aufzeichnungen für die Auswertung in Tabellenkalkulations-Formulare zu übertragen. Diese boten nur begrenzte Möglichkeiten für Analysen. Zudem waren die Daten und Auswertungen dort sowohl von der Unternehmens-IT als auch von den Automatisierungssystemen isoliert. So konnten sie nicht ohne Weiteres für steuernde Maßnahmen verwendet werden.
Flexibles Überwachungssystem gefordert
Um die Anlageneffizienz besser kontrollieren und auf einem hohen Niveau halten zu können, entschloss sich die Geschäftsführung, diesen datentechnischen Inselbetrieb durch eine moderne integrierte Gesamtlösung zu ersetzen. Dazu sollte die komplette Abfüll- und Verpackungslinie mit einem übergreifenden Leitsystem versehen werden. Um die an sich gut funktionierenden Teilsysteme nicht ändern zu müssen, sollte sich die Lösung ohne Eingriffe in deren SPS-Programmierung realisieren lassen.
Die Anforderungen waren umfassend: Das System sollte die zentrale Überwachung der gesamten Anlage erlauben und die Auswertung der Gesamtanlageneffektivität (Overall Equipment Effectiveness; OEE) ermöglichen. Neben anderen Berichten sollte das Reporting auch die Auswertung von Stillstand und Mikrostillstand (bis zehn Sekunden) ohne nennenswerten Aufwand bis zur Anzeige eines Paretodiagramms umfassen. Der Zugriff auf das System sollte einerseits standortunabhängig über einen Web-Server erfolgen können, andererseits jedoch durch RFID-Login gegen unbefugten Zugriff geschützt sein.
Offene Softwarelösung, perfekt angepasst
Den Projektauftrag gewann Kropf Solutions mit ihrer Niederlassung im tschechischen Cheb. Das auf Industrieautomatisierung spezialisierte Unternehmen arbeitet bereits seit mehr als 20 Jahren eng mit COPA-DATA zusammen. „Die Software zenon ist auf flexible, offene und zuverlässige Anwendungen zugeschnitten“, sagt Ronny Duchek, Leiter der technischen Abteilung bei Kropf Solutions, der das Projekt leitete. „Auf dieser soliden Basis schaffen wir für unsere Kunden maßgeschneiderte Lösungen mit hoher Dynamik und Ergonomie.“
Erster Teil der Gesamtlösung für Jan Becher war die Zusammenfassung sämtlicher Teilsysteme innerhalb der Abfüll- und Verpackungslinie über Gateways in ein übergreifendes Ethernet-Netzwerk. Dieses bindet die Produktionsanlagen an einen zenon Server an, der auch die Verbindung zum unternehmensweiten Netzwerk darstellt. Für direkte, maschinennahe Eingriffe steht ein industrielles Multitouch-Panel zur Verfügung. An diesem befindet sich auch ein RFID-Leser, über den die Benutzeranmeldung in zenon erfolgt.
Vor der Freigabe für den produktiven Betrieb unterzogen Kunde und Systemintegrator das zenon Projekt umfangreichen Tests. Dabei tauchten auch immer wieder neue Anforderungen auf, an die in der Definitionsphase niemand gedacht hatte. Diese ließen sich jedoch durch die offene Struktur von zenon problemlos in die beinahe fertige Implementierung integrieren, sodass Kropf Solutions nach sehr kurzer Testphase eine praxisreife Lösung übergeben konnte.
Voller Überblick ohne Handarbeit
Das auf zenon basierende Leitsystem hat sämtliche der bisher erforderlichen manuellen Aufzeichnungen überflüssig gemacht. Vollautomatisch zeichnet es permanent die Betriebszustände aller Anlagenteile auf, sekundengenau und ohne die Möglichkeit menschlicher Fehler, wie z. B. von Zahlendrehern. Ebenso entfällt das bisher nötige Übertragen der Daten. Diese befinden sich sofort nach dem Erfassen in der Datenbank, wo sie unmittelbar für sämtliche Auswertungen zur Verfügung stehen.
Die Gesamtanlageneffektivität wird im gesamten Konzern ab sofort einheitlich berechnet. Anhand vorgegebener Formeln programmierten die Anwendungsspezialisten von Kropf Solutions im integrierten SPS-System zenon Logic die entsprechenden Auswertungen. Diese werden in unterschiedlichen Formen als Live-Übersicht oder Trend-Diagramm dargestellt, einerseits am Panel in der Produktion, andererseits aber mit Hilfe von Web-Clients in verschiedenen Büros. Stillstände und erzwungene Reduktionen der Geschwindigkeit in der Abfüllanlage können dort in Detailansichten, aber auch in Form eines Paretodiagramms betrachtet werden.
Wesentlich für Ablauf und Steuerung des Gesamtbetriebs, aber auch als Grundlage für Folgeentscheidungen im Konzern, sind die automatisierte Erstellung und der Versand von Tages- und Monatsberichten.
Datenbasis für weitere Optimierungen
„Durch seine Vielseitigkeit und hohe Anpassungsfähigkeit an unsere spezifischen Anforderungen und sein benutzerfreundliches Design hat zenon unsere Produktionsabläufe transparenter gemacht und das Personal von lästigen Dokumentationspflichten entlastet“, sagt Bryzgal. „Als nächsten Schritt möchten wir das System dazu nutzen, unsere Produktionsabläufe weiter zu optimieren.“
-
Dank zenon konnten die Ingenieure von Kropf
Solutions alle unsere Anforderungen umsetzen, auch solche, die erst in der Testphase auftauchten.Tomáš Bryzgal | Plant Director Jan Becher - Karlovarská Becherovka, A.S
Download
-
Success StoryBecherovka_SUS_DE.pdf