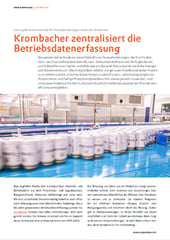
Krombacher centralizes its plant data collection (Germany)
Success Story in Inglese
Oggi i birrifici devono affrontare una serie di sfide che influiscono sui loro processi produttivi e commerciali, come la fluttuazione dei prezzi e la disponibilità di materie prime come il luppolo e il malto. Inoltre, i birrifici consumano molta energia e acqua. Di conseguenza, è sempre più importante identificare con precisione il costo di ogni singola bottiglia e capire la fonte di questi costi. Allo stesso tempo, crescono le richieste di pratiche di produzione sostenibili. Per affrontare queste sfide, sono necessari approcci innovativi che supportino continui miglioramenti dell'efficienza produttiva.
Una bottiglia di birra riempita genera una notevole quantità di dati operativi provenienti dai processi di produzione e logistica. Questi dati possono fornire informazioni sul consumo energetico, sui tempi di inattività, sulla quantità di riempimento e molto altro ancora. Per garantire una gestione efficace di questi dati, è necessario essere in grado di raccoglierli in modo efficiente e fornire una reportistica chiara. I sistemi preesistenti di Krombacher non erano più in grado di soddisfare questi elevati standard di raccolta dei dati dell'impianto. Il birrificio ha deciso di investire in un sistema completamente nuovo e, da allora, Krombacher utilizza zenon di COPA-DATA.
La raccolta dei dati di produzione ha dei vantaggi interni per le aziende. Un buon sistema di analisi e reporting può aiutare le aziende a misurare e migliorare l'efficienza delle loro macchine. Fornisce previsioni sui tempi di riempimento di determinati lotti, compresi i tempi di cambio formato o di pulizia e, quindi, facilita la pianificazione. I produttori sono inoltre tenuti per legge a effettuare il reporting dei dati. Tuttavia, il grande volume di dati raccolti può rappresentare una sfida significativa. Maggiore è il numero di dati raccolti, più complessa è la preparazione dei report.
Dopo 15 anni, il sistema di raccolta dei dati operativi di Krombacher non era più aggiornato e richiedeva molte operazioni manuali per preparare analisi e report. I dati aggiuntivi dovevano essere inseriti manualmente in Excel utilizzando script di Visual Basic. Non era possibile preparare report PDF automatizzati o distribuire i dati a livello centrale. Per la visualizzazione era disponibile un'applicazione separata. Tuttavia, questa applicazione presentava uno svantaggio: i dati dovevano essere mantenuti e aggiornati separatamente.
Qualsiasi modifica al sistema costava a Krombacher molto tempo e fatica. Il vecchio sistema proveniva dal fornitore delle macchine ed era configurato specificamente per le macchine di riempimento. Questa personalizzazione è diventata rapidamente un ostacolo non appena si sono rese necessarie delle modifiche. Non era facile apportare modifiche e, in alcuni casi, Krombacher non era in grado di farlo da sola. È stato inoltre difficile integrare altre macchine, come stazioni di aria compressa o sistemi energetici, perché il sistema e il suo funzionamento erano configurati specificamente per le linee di riempimento. "Quando il nostro ultimo fornitore di servizi ha terminato l'assistenza dopo 15 anni e il panorama dei server era così obsoleto da non poter più funzionare con gli attuali sistemi Windows, abbiamo deciso di cambiare sistema", afferma Marc-Philipp Böttler, responsabile delle operazioni e dell'ingegneria di Krombacher.
Krombacher ha scelto di lavorare con il system integrator Actemium, che ha introdotto la piattaforma software zenon di COPA-DATA. Uno dei motivi era che il nuovo sistema non si sarebbe più concentrato solo sul riempimento. Dal chicco di malto alla bottiglia riempita e confezionata, le fasi del processo dovevano essere il più possibile efficienti e trasparenti. Fino a quel momento, le macchine della birreria, dell'area fredda, del riempimento e della logistica di Krombacher funzionavano con sistemi diversi. Di conseguenza, una reportistica completa basata sui dati era possibile solo con un notevole sforzo manuale. Il compito di Actemium è stato quello di standardizzare le attività di raccolta dei dati e il panorama dei sistemi, rendendo così più semplice il reporting per il cliente. Inoltre, tutti i dati raccolti dovevano essere disponibili a livello centrale.
Nella scelta del nuovo sistema, Krombacher ha deliberatamente optato per un sistema aperto, in modo da poter apportare modifiche in modo indipendente. zenon ha colpito anche per la sua rappresentazione grafica, la chiara visualizzazione e la facilità d'uso: in altre parole, un hub di dati centrale che può essere personalizzato a seconda delle esigenze e che funziona comunque come una soluzione pronta all'uso. Inoltre, zenon fornisce un'importante interfaccia di comunicazione con il principale strumento di Business Intelligence (BI) di Krombacher.
La nuova linea di riempimento lattine installata durante la fase di progetto ha funzionato come progetto pilota. Stefano Margarucci, BU Manager di Actemium, spiega: "La nuova linea di riempimento lattine è servita come progetto pilota per noi, poiché è stata installata durante il progetto. Il vantaggio è stato che non c'erano dati pregressi da integrare. Questo ci ha permesso di sviluppare la struttura del sistema da zero".
Tuttavia, il trasferimento del sistema ad altre linee e aree ha comportato alcune sfide. Stefano Margarucci aggiunge: "L'apparecchiatura esistente riempiva bottiglie, non lattine. Ciò significa che per estendere il sistema abbiamo dovuto implementare ulteriori passaggi e aggiornare i simboli. Questa rielaborazione ha richiesto molto impegno".
zenon funziona ora su dodici linee, ognuna con diverse macchine. Sono collegati più di 262 controllori logici programmabili (PLC) per le vasche di ammostatura, i serbatoi di fermentazione o le etichettatrici. Circa 230.000 variabili sono registrate e valutate in più di 350 report. La connessione all'applicazione SAP ERP consente al cliente di interrogare gli ordini pianificati e di inviare i dati fiscali. Inoltre, dai dati è possibile calcolare previsioni, ad esempio per i tempi di esecuzione dei singoli lotti o per i tempi di cambio formato o di pulizia, oppure registrare e confrontare i valori misurati con quelli target.
"Apprezziamo molto il sistema aperto e i suoi vantaggi. Ci dà flessibilità quando acquistiamo e colleghiamo nuove macchine di produttori diversi. Possiamo apportare noi stessi piccole modifiche e rispondere così più rapidamente ai trend", afferma Marc-Philipp Böttler. "zenon non è solo un sistema di raccolta dei dati operativi. Supporta anche il controllo e la visualizzazione. Questo porterà a nuove sinergie che potremo sfruttare in futuro, ad esempio nella logistica".
Nonostante la digitalizzazione e i progressi dell'automazione, le persone rimangono un fattore essenziale per il successo di questo tipo di progetti. "A cosa serve la tecnologia più moderna se non viene accettata dalle persone che devono utilizzarla?", afferma Thomas Will, responsabile dell'automazione presso Krombacher. "Fortunatamente abbiamo potuto contare su un team esperto". Coinvolgere i dipendenti fin dalle prime fasi è importante perché aiuta a sviluppare l'accettazione dei nuovi sistemi e, quindi, garantisce il successo del progetto.
Actemium e Krombacher stanno attualmente lavorando per garantire che in futuro sia possibile raccogliere, valutare e presentare in formato visivo un numero ancora maggiore di dati. Gran parte dei costi di produzione dovrebbe essere determinata automaticamente e valutata su base specifica del lotto. A questo scopo, il processo di produzione dal malto in grani al pallet finito deve essere ripercorso utilizzando un albero dei lotti. Esiste anche un ulteriore potenziale per la visualizzazione dei processi effettivi di riempimento e logistica, che potrebbe includere il tempo rimanente per il lotto corrente fino al passaggio al prodotto successivo. È in fase di sviluppo anche l'analisi delle cause principali. In futuro, i report automatizzati identificheranno la macchina dell'impianto di produzione che ha effettivamente causato il fermo macchina. Questo aiuterà a identificare il potenziale per aumentare l'efficacia complessiva delle apparecchiature (OEE).
We really appreciate the open system and its benefits. It gives us flexibility when purchasing and connecting new machines from different manufacturers. We can make minor adjustments ourselves and thus respond more quickly to trends.
Success Story in Inglese